There are generally three situations in the emergency braking of a car:
1. The front wheel is locked and dragged first, and then the rear wheel is locked and dragged.
2. The rear wheel is locked and dragged first, and then the front wheel is locked and dragged.
3. The front and rear wheels are locked and dragged together.
Facts have proved that the front and rear wheels are locked prematurely, which greatly reduces the braking deceleration of the vehicle and causes problems such as sideslip (I will not go into details here). Therefore, each manufacturer has a common specification when calibrating the brakes: The front and rear wheels must be locked together.
Next, let's take a look at the parameters involved in the braking force of a certain model. Are these parameters related to front-wheel drive or rear-wheel drive?
As shown in the figure above, assuming that the road surface adhesion coefficient is fixed, the front and rear wheel shoes have the same friction coefficient and the area is roughly the same, then the friction force applied to it, no matter whether it is no-load or full-load, the front wheel shoes are larger than the rear. Wheel shoe. In other words, the front wheel wear should be greater than the rear wheel wear, and the summed ratio is between 2:1 and 3:1, and it has nothing to do with front-wheel drive or rear-wheel drive.
Therefore, under normal conditions, the front wheel shoe is replaced 2 to 3 times, and the rear wheel shoe will only be replaced once.
If the rear wheel shoe wears faster than the front wheel, consciously check the braking ability of the front wheel shoe and the disc surface, there must be a problem with your braking system. Drift and sideslips are also more likely to occur under hard braking conditions.
And if the replacement speed of the front wheel shoe exceeds this standard, you should also automatically check your braking system, but the key is on the rear wheel. Otherwise, under the emergency braking situation, it is more likely to lose control of the direction and allow severe.
hint:
The main point is to check the front and rear wheel sub-pumps, the gap between the front and rear wheel shoes and the brake disc, the exhaust condition of the front and rear wheel brake pipes, and even whether there is residual air in the ABS pump.
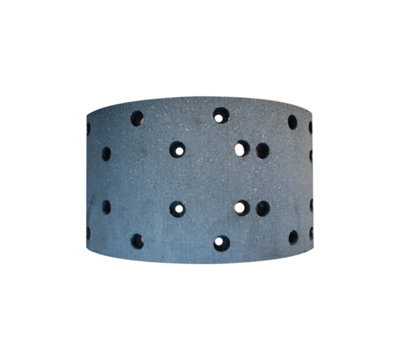
The common material of brake shoes is my country's gray cast iron 250 specification, abbreviated as HT250. The main chemical components are: C (3.1-3.4), Si (1.9-2.3), Mn (0.6-0.9), and the hardness is between 187-241. The brake shoe blank is precision cast and heat treated to improve the internal stress during the casting process, reduce deformation and cracking, and improve the machining performance of the casting. After screening, the blanks that meet the requirements are machined. The procedure is as follows:
1. Rough turning and large outer surface
2. Rough car hole
3. Rough car small round end face, side and right brake face
4. The left brake surface of the rough car and each inner hole
5. Large outer surface of semi-finished car, left brake surface and each inner hole
6. Semi-finished small outer surface, end face, middle hole and right brake surface
7. Fine turning groove and right brake surface
8. The left brake surface and the small round end face of the fine turning, the bottom round surface of the left bottom of the fine turning, the inner hole chamfering
9. Drilling and deburring, blowing iron filings
10. Storage
Processing requirements for truck brake lining
Brake shoes are an important part of the braking system. Good brake shoes provide stable braking without noise and vibration. Therefore, the processing requirements are higher, as follows:
1. The brake shoe is a cast product, and the surface is required to be free from casting defects such as blisters and pores, so as to ensure the strength and rigidity of the brake shoe and avoid accidents under the action of external forces.
2. Two braking surfaces are used when braking, so the precision of the braking surface is relatively high, and others can be
Ensure azimuth accuracy.
3. High temperature will occur during braking. The center of the brake disc should be designed with an air duct to facilitate heat dissipation.