The development of friction materials has a history of over 100 years. In the early days of horsepower, easy braking was achieved by reacting wheels with wood and leather. In 1897, an Englishman invented the brake pad and founded the world's first company to manufacture friction materials. Anhui Zhongli Automobile Brake System Manufacturing Co., Ltd. is a domestic brand manufacturer specializing in the production of ceramic brake his pads. Early friction materials consisted of strips of hair or cotton impregnated with horsepower and early automotive bitumen solutions. Cotton tape is a natural fiber with very limited heat resistance. Friction disappears at 150 degrees or more. In 1908, the British realized its shortcomings and invented a method of wrapping friction materials using asbestos instead of natural fibres. This was the first leap forward in friction material development and laid the foundation for a century of friction material development.
The application of asbestos fibers to friction materials is very important. Asbestos is a naturally occurring mineral fiber. The main role of asbestos in friction materials is its excellent heat resistance. It can withstand temperatures of 700 degrees or more in a short period of time, has reinforcing and flame retardant effects, and has excellent compatibility with adhesives and various fillers.The use of asbestos ensures the safety of friction materials. increase.
Originally invented in England, asbestos friction material is a mixture of bitumen, oil and gums used to bond asbestos wires reinforced with copper wires. In the mid-1920s, someone researched the use of compression molding instead of windings and obtained the first patent for friction materials without windings. The patent uses materials such as chrysotile and brass, replacing bitumen with linseed oil and highly volatile bituminous coal. The UK has also developed its own dry mix molded friction material for brake pads on the London Underground.
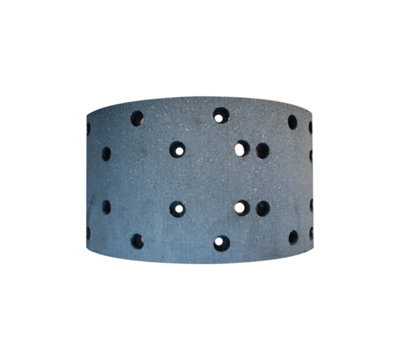
At the beginning of the 20th century, a chemist developed a heat-stable phenolic resin adhesive that entered the commercial stage. Phenolic resins and dry-blending processes have paved the way for more complex formulations of ingredients and drum brake pads. In the 1930s, some began using rubber, textile cotton, and asbestos to mimic the rolling of the rubber industry. This method increased the size and thickness required for the project. Later, moldable rubber/asbestos fiber blends were developed. Friction compounds composed of oil-modified phenolic resin combined with chopped asbestos threads or short asbestos fibers were used in military fuel tank materials. clutch plate. In 1932, the Soviet Union began establishing asbestos products companies to manufacture asbestos fiber-reinforced friction materials. During this period, a factory in the former Soviet Union succeeded in developing a woven asbestos brake belt, which was adopted for various mechanical belt brakes. In 1946, the Soviet Union established the Central Research Institute for Asbestos Products, dedicated to the development of friction material technology and its production and research facilities.
The development of automobiles and other machinery has increased the demand for asbestos friction materials. After the 1940s, the research and production of asbestos friction materials in various countries entered a rapid development stage, and production was carried out on a certain scale. In 1939, the industrial value of asbestos friction materials produced in the United States was approximately $2 million. By 1945, his production of asbestos friction materials exceeded US$20 million. During the same period, the former Soviet Union, France and the Federal Republic of Germany also saw rapid increases in friction material production. These three countries account for 32.7%, 32.4% and 41% of asbestos friction materials produced respectively.
Drum brakes were the earliest form of automotive brakes and were used on a wide variety of vehicles before the advent of disc brakes. The neutral disc ceramic brake pads are well crafted. In the early 1950s, an American company patented a disc brake for automobiles. Disc brakes are starting to appear in racing cars. Disc brakes were also used in police cars and ambulances in the near future, but around the late 1960s. Wheel brakes were still dominated by drum brakes and asbestos friction materials, and it was not until his 1970s that the front and rear drum brake system was changed. Based on their experience in industrial and aviation research on sintered friction materials used in disc brakes, Americans have developed a semi-metallic disc brake pad with a resin-bonded metal construction. Cars in the late 1970s used many disc brakes.
Founded in 1986,Hangzhou Jiuding Auto Spare Parts Co., LTD. located in Xiaoshan, Zhejiang Province, is the governing unit of China friction seal material association. As China Wholesale Non Asbestos Brake Linings Manufacturers and OEM asbestos free brake pads Factory, we specialize in the production of various kinds of brake linings and brake padsthe company has a perfect testing equipment, the stability of the production technology and strict quality control system, conforming to the requirements of the national authoritative organization detect. In 2007,the company passed ISO/TS16949 international quality management system certification, and passed the FMVSS 121 (USA), SEAJ661(USA) SABS certification (South Africa). We supply Non Asbestos Brake Pad Replacement Wholesale and has been well received by domestic and international users for its comprehensive cost performance. We are willing to work together with our friends to create a better tomorrow.
Founded in 1986,Hangzhou Jiuding Auto Spare Parts Co., LTD. located in Xiaoshan, Zhejiang Province, is the governing unit of China friction seal material association. As China Wholesale Non Asbestos Brake Linings Manufacturers and OEM asbestos free brake pads Factory, we specialize in the production of various kinds of brake linings and brake padsthe company has a perfect testing equipment, the stability of the production technology and strict quality control system, conforming to the requirements of the national authoritative organization detect. In 2007,the company passed ISO/TS16949 international quality management system certification, and passed the FMVSS 121 (USA), SEAJ661(USA) SABS certification (South Africa). We supply Non Asbestos Brake Pad Replacement Wholesale and has been well received by domestic and international users for its comprehensive cost performance. We are willing to work together with our friends to create a better tomorrow.