In most cases, friction materials rub against various metals. It is generally believed that under friction conditions, materials with a coefficient of friction greater than 0.2 are called friction materials.
According to its friction characteristics, the material is divided into low friction coefficient material and high friction coefficient material. Materials with a low coefficient of friction, also known as anti-friction materials or lubricating materials, are used to reduce power losses in mechanical motion, reduce wear and extend service life of mechanical components. Materials with a high coefficient of friction are also known as friction materials (referred to as friction materials).
According to the work function, it can be divided into two categories of friction materials: transmission and braking. For example, the clutch plates of the transmission transmit the power generated by the engine to the drive wheels through the fitting and disengagement of the clutch friction surfaces in the clutch pack, so that the vehicle starts to travel. Brake pads (divided into disc and drum brake pads), the brake pads are connected to the brake disc (drum) through the vehicle braking mechanism to slow or stop the moving vehicle.
2. According to the shape of the product, it can be divided into brake pad (disc type, drum type), brake belts, brake pads, clutch discs, and isotropic friction pads. The disc is flat and the drum is curved. Brake shoes (train brake shoes, oil rigs) are a curved product, but they are much thicker than normal curved brake pads, ranging from 25 to 30 mm. Brake bands are commonly used in agricultural and construction machinery and are soft friction materials. Clutch plates are usually ring-shaped items. Heterogeneous friction discs are mainly used in various construction machinery, such as friction presses, electric hoists, etc.
3. According to the material of the product, it can be divided into two categories: asbestos friction material and non-asbestos friction material.
One, asbestos friction materials are divided into the following categories: one, asbestos fiber friction materials, also known as asbestos velvet friction materials. Production: various brake pads, clutch pads, synthetic train brake pads, asbestos velvet rubber belts, etc. b, asbestos linear friction materials. Production: wound clutch plates, chopped asbestos thread friction materials, etc. c, asbestos fabric friction materials. Production: Manufacture of laminated boring machine brake pads, brake belts, clutch panels, etc. d, asbestos woven friction materials. Production: The manufacture of oil-impregnated or resin-impregnated brake bands. Oil rig brakes, etc. B. Non-asbestos friction materials are divided into the following categories: one, semi-metal friction materials. Disc brake pads for automobiles and heavy vehicles. The composition of the material usually contains about 30% to 50% ferrous metals (eg steel fibers, reduced iron powder, foamed iron powder). Therefore, semi-metallic friction materials are proposed. This is the first asbestos-free material to be replaced with asbestos. Its characteristics: good heat resistance, high absorption power per unit area, large thermal conductivity, and can be used in high-speed and heavy-duty vehicle braking conditions. However, it has the disadvantages of high braking noise, cracking at the angle, etc.
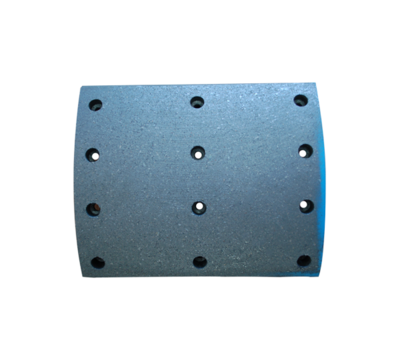
b, NAO friction material. Broadly speaking, it refers to non-asbestos-non-steel fiber friction materials, but the discs also contain small amounts of steel fibers. The base material in NAO friction materials is in most cases a mixture of two or more fibers (inorganic fibers with a small amount of organic fibers). Therefore, the NAO friction material is a non-asbestos hybrid fiber friction material. Typically, the brake pads are chopped fiber type friction pads, and the clutch plates are continuous fiber type friction pads.
c. Powder metallurgy friction materials. Also known as sintered friction materials, iron-based, copper-based powder materials are passed, molded, mixed and sintered at high temperatures. Suitable for braking and transmission conditions at higher temperatures. Such as: aircraft, trucks, heavy construction machinery braking and transmission. Advantages: long service life; Disadvantages: high product price, high braking noise, heavy and brittle, high wear and tear, carbon fiber friction material. A friction material made of carbon fiber as reinforcement. Carbon fiber has high modulus, thermal conductivity, and heat resistance. Carbon fiber friction materials are the best of all types of friction materials. Carbon fiber friction pads have high absorption capacity and light specific gravity per unit area. It is especially suitable for the production of aircraft brake pads. Also used the brake pads of some foreign high-end cars. Due to its high price, its application range is limited and its output is small. In the carbon fiber friction material component, in addition to carbon fiber, a compound of graphite and carbon is used. The organic binder in the composition is also carbonized, so the carbon fiber friction material is also called carbon-carbon friction material or carbon-based friction material.
PREV:Evolution of friction materials
NEXT:What is the difference between brake pads and brake discs?
NEXT:What is the difference between brake pads and brake discs?